
Pottery Art in India
Pottery art in India is as ancient as the country itself. According to archaeological evidence, it was prevalent even during the Indus Valley Civilization. The exact time period when it came to Bengal is unknown, but what helped it grow and develop here was the fertile alluvial soil of the Ganges. Today, West Bengal is one of the largest producers of terracotta pottery in the country. The art form is spread all over this state, but Panchmura pottery has its own unique appeal, beauty and popularity.
The Famed Panchmura Pottery :
Panchmura is a small village in the Bankura district of West Bengal, approximately 300 km from Kolkata. Most of us will find it easier to familiarize ourselves with this place and the art form that has existed and grown here if I simply mention the infamous ‘Bankura Horse’. This is where the typical horse, proudly displayed in many homes, is crafted. But ‘Bankura Horse’ is only one of the artifacts that churn out of the hands of the kumbhakaras or artisans of this village.
In our country handicraft items are sold at prices above reasonable in showrooms. However, it is a sad fact though that these art forms are in a miserable condition in most parts of India. A considerable lot has been said about this, but significant little done for their survival and glorification.
It was under such dire circumstances that the kumbhakaras (potters) of Panchmura, together with enterprising individuals, realized that they have to be the masters of their destiny if they wanted to prevent the extinction of the centuries old Bengal terracotta art. And thus the struggle for existence began.

Giving shape to the Clay :
The Making :
“The most important raw material for pottery is clay.” Terracotta is the hard, partially burnt clay without any moisture, used for pottery. Panchmura artisans have always taken care that even when operating under losses, no compromise should be made on the mati or clay. They use the finest quality of clay available on the banks of the Ganges near Kolkata, commonly known as gangamati (clay from the Ganges). It is quite interesting that the artists even take care of the age of the mati. “The older the alluvial clay, the better the quality.”
Once the mati (clay) is received, the actual work begins. It is a long process, taking up days, and at times even months, to complete. Even today, the age old potter’s wheel or chak is used for construction. Initially few selective articles were made. These consisted of various types of pots and other usable products. With innovation and experimentation, the artists began the production of other shapes which were decorative in nature. This was the stage of moving away from satisfying basic requirement to being an art for the market. It no more remained restricted to the village. Complicated designs were introduced, and the infamous ‘Bankura Horse’ created. The characteristic feature of this is that the entire product, say the horse, is not made together, unlike the pots that were simpler to make. It consists of various pieces which are constructed individually, on the wheel, and then joined together to give the final shape. They are then scraped and made even to give the smooth finish. Smaller and intricate parts are handmade and joined to the main body. This therefore marked the beginning of an art form that required great skill and expertise.
The tedious procedure does not get over here. After the basic products are made, they have to be dried. But not under direct sun, as it may lead to minute fractures and result in easily breakable forms. They are left in an open space for days for the moisture to completely evaporate. When this is done, the final baking takes place.
The furnace or bhati used for baking has to be carefully constructed. Authentically, the bhati is made by digging the ground in a circular shape (nowadays electric furnaces are becoming popular though that saves labor as well as cost and can be used repeatedly unlike the handmade furnace that can be used only once). Then it is lined with bricks and filled with coal (by well to do artisans), cow dung cake or wood and bhusa, that is cattle feed, (by poorer artisans). The art pieces are then carefully placed in the furnace, against one another. It is then lit and the opening of the bhati sealed. Depending on the products and the artists’ choice of color and strength, the heating takes place. Usually under normal circumstances, this is an overnight procedure, taking about 8-10 hours. Then the furnace is opened, the baked products taken out carefully and left to cool for 4-5 hours. The art forms have by now got their color that we see in the market, the true orange color of terracotta and it is ready for sale.
Emergence of Panchmura Clay Artwork :
“For a very long time, Bengal terracotta art was restricted within the state and in select places only,” Bipin, who has a shop selling Panchmura pottery, says. “One could purchase only at the time of annual fairs”. Unarguably, the art form was losing its prominence and popularity due to lack of availability and an organized market. The re-emergence of this art took place when groups of people formed cooperatives and came to the forefront. These self financed small groups studied the market, the demand for terracotta, and deducted that a profitable business could thrive. This would not only provide a regular source of income to the adroit kumbhakaras but also to the sellers.
Retail outlets were thus set up at various places. Today many cities in West Bengal, as well as other parts of the country, have outlets which sell Bengal terracotta artifacts. The heartening fact is that these are also being exported now, and the market is only becoming larger and more diverse, as art lovers all over are recognizing and appreciating the delicately and beautifully made forms.
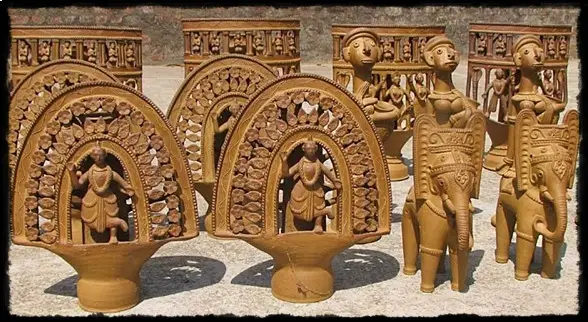
Much to the dismay of the traditional artists, terracotta is being colored today. Metallic color has become quite common, apart from stone and red brick colors. Terracotta is always colored under direct sunlight to acquire the glaze and shine that results from color mixed in proportion to spirit. For some kumbhakaras, who have lived with the art, “coloring is a loss of self respect”, or as they say it, the morjada, of the art form. As mere, most of the times, helpless artisans, they have no choice but to meet the demand of their customers.
Survival of the fittest, the law of the world, is witnessed in this instance. The constant effort to keep afloat goes on. If we agree that compromise is the rule of any game, then for these artists it is a mode of life. As patrons and lovers of this art form, we can at the least make an effort to help keep this art alive. The next time I go to one of these outlets, I will definitely get them as gifts for my friends and family members. And I am sure they will only be too happy to flaunt authentic Bengal terracotta in their homes and be noticed and appreciated by everyone.